The Best Alternative To Industrial Gate Valves
10-08-21
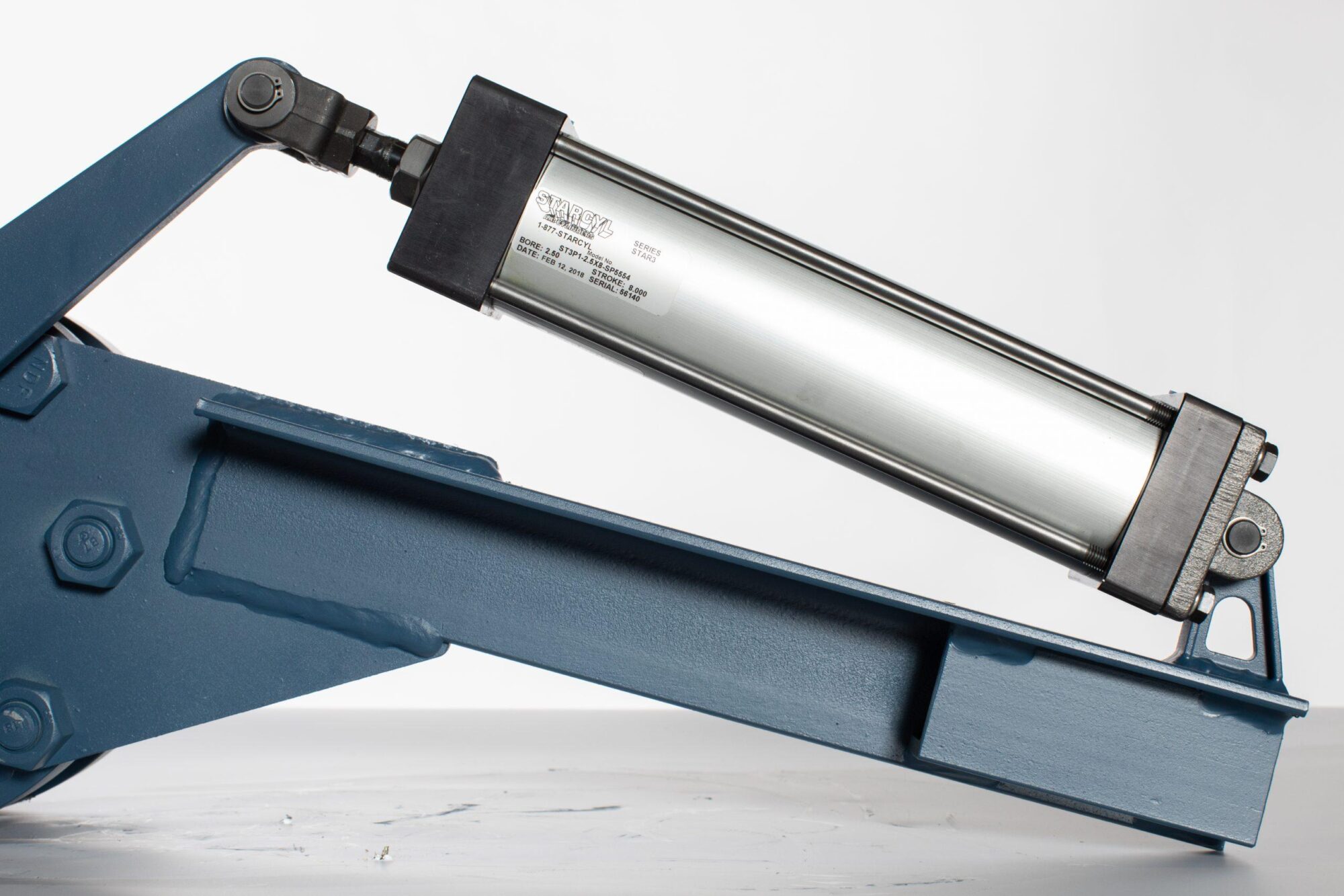
Popularity in industrial solutions many times means common, not best. The industrial gate valve is often selected for use but wears out and dirt damages the bushings. This drives the serious manager to look for an alternative solution.
Did you know the rotating disc valve does the same job with less wear and damage?
This guide will help you find the best alternative to the industrial gate valves. We’ll help you understand what breaks down in the standard industrial gate valve. We’ll also cover the alternatives and why the rotating disc valve is a great choice.
Industrial Gate Valves
Industrial gate valves allow for a pass-through of fluids or gases when open. When closed, the flow stops, isolating the liquid from the system.
There are two kinds of gate valves:
Rising Stem
The disc resides at the base of the stem. When the handwheel turns, the stem rises above the handwheel, lifting the disc into the bonnet.
Non-Rising Stem
The disc screws onto the bottom of the stem. When the handwheel turns, the stem rotates and the disc climbs the threads into the bonnet.
Both types of gate valves open the pipe for a non-regulated low-pressure flow. Non-regulated because it’s made to only be open or closed.
Wear and Damage
The disc or its seat rings can get worn and need replacement maintenance as part of its life cycle. This is due to the fine fit they must have to seal. The disc can also get worn if it is not open or closed all the way.
The gate valve is not made to be a throttle. When the disc is not completely open, the pressure inside of the valve increases. This can cause high-velocity turbulence and damage the disc or the seal rings.
Alternative Valves
The common alternative valves include the globe, ball, butterfly, and check valves. While each has a strength, it also brings a new weakness to bear.
Globe Valve
Unlike the gate valve, this valve can control the flow. The position of the disc inside of the valve regulates the flow of the fluid or gas. Instead of the disc being vertical, it pushes down on the ring seat in a horizontal position.
Gate valves insert into the pipeline in any direction. Globe valves differ in having a flow direction marked for installation. This is due to the rise and lowering of pressure with incremental handwheel turns.
The disc position and movement can create a big change in pressure. When the pressure is high, the globe valve takes a significant amount of force to close.
Ball Valve
This type of valve is ideal for regulating gases due to its sealing ability. These airtight seals can handle up to 700 bars of pressure. They can also handle high temperatures up to 200°C.
They can only rotate to 90-degrees for the full opening or closing of the valve.
This valve is inexpensive, so many budget for replacement valves. The most common cause of replacement is from the seat of the ball valve eroding.
When it comes to fluids, particles in the fluid collide with the ball and may cause abrasions and leaks. But the ball valve is often used as a shut-off for corrosive fluids.
Butterfly Valve
The core design of the valve is to regulate flow. Like the ball valve, it has a 90-degree rotation. But this valve is a disc, not a ball, so it requires a seat.
The operation of this valve can be electronic, manual, or pneumatic. This valve is very accurate and reliable in controlling flow. But the pressure can change as the valve is always presented to the flow.
These are often used in the food and pharmaceutical industries. They can handle low heat and low pressure.
The Best Alternative Valve
When it comes to industrial valves, there is one choice that makes the best gate alternative. The rotating disc valve is tougher, stronger, and more reliable than gate valves. An actuating arm moves the disc into its open or shut position. A person can’t leave it partway open. This means the pressure is close to stable at all times.
The design clears out and shears away process material. Particles can’t build up to cause wear. This allows the valve to achieve a tighter seal and lower the leak rate below that of other valves with each pass.
This process reduces failures, maintenance, and replacements. This means companies no longer have to buy the cheapest part with a heavy replacement budget. Instead of each use wearing down the seal, the rotating disc valve improves its seal with each use.
One case study showed the client needing a valve to handle 250 open and close cycles per year. Every six months after 125 cycles, the company installed a cheaper replacement valve. When the rotating disc valve got installed, it handled the 250 cycles per year for 25 years.
When looking for an alternative valve, most individuals consider function. But other values that impact the valve’s life cycle need consideration. The most obvious must include process downtime, maintenance costs, and life cycle longevity.
To understand the full impact of a replacement product, all details need review. Also, every associated valve expenditure must enter into the total operational cost.
The Better Value Alternative
Industrial gate valves are pass-through inline valves that have several alternatives available. The common ones include the globe, ball, and butterfly valves. But the best alternative valve is the rotating disc valve.
This valve brings the same function to bear with improvements. The design reduces maintenance, replacements, and improves its seal with each cycle. This self-cleaning method clears out the process materials and extends the life cycle.
It’s time to consider a rotating disc valve for your next gate valve replacement. You’ll be able to select from off-the-shelf valves and custom valves. Contact us to learn about the longest-lasting, best-valued replacement valve.