Valve Testing Methods And Standards: A Guide
01-14-22
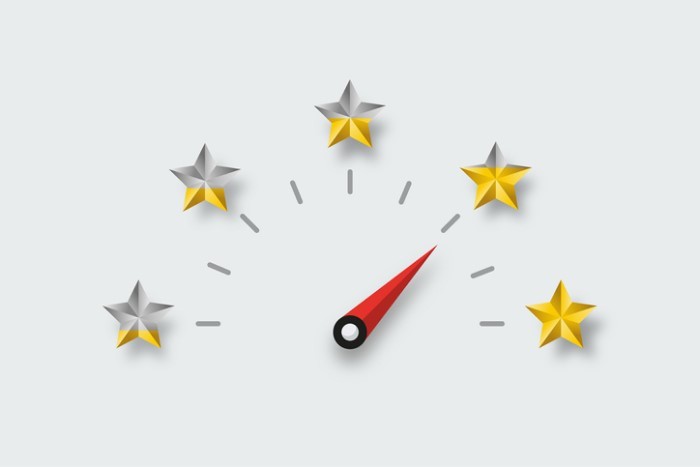
Did you know that before 1930, valve pressure categories were just standard, medium, or extra heavy? To make matters worse, there was no agreed upon definition for any of those classes! Some manufacturers would list the amount of pressure at which a valve would burst in the product description, but other than that there was very little regulation.
Fortunately, today there are far more safety standards and valve testing methods used to measure valve quality. This is due to the efforts of organizations such as the American National Standards Institute (ANSI) and the American Petroleum Industry (API).
Keep reading to learn about the standards and testing methods used to ensure a safe and efficient product.
Valve Standards
Before 1968, most types of valves were not supposed to leak at all. Many valve manufacturers still aim for zero leakage, but the standards are a bit more lenient than they used to be for some designs.
Here are some of the most common standards that currently apply to valves.
API 598
This standard covers valve testing, inspection, and pressure test requirements for ball, butterfly, gate, glove, and check valves. It specifies the acceptable rates of leakage for various sizes and materials. The API 598 standard applies especially to the oil and gas industries.
These standards need to be met before the valve is shipped from the manufacturer.
API 607
This applies to test methods and performance evaluation of soft-seated quarter-turn valves when there is exposure to fire conditions. It is important to test for these conditions to ensure that a valve will not explode or melt in case of an accident.
The ANSI created pressure classes for valves, which range from 150 to 900 and beyond. Testing a valve needs to take into account its pressure class.
API SPEC 6D
This is an international testing standard that applies to ball valves, check valves, and plug valves. It specifies the requirements and provides recommendations for the design, manufacture, testing, and documentation of valves.
BS 759-1
This standard applies to valves, gauges, and other fittings associated with boilers. Testing methods are used for the valve, its mounting, and any other fittings it might have.
MSS-SP 55
The MSS is the Manufacturer’s Standardization Society. It provides standards for valves which are commonly used fully open or fully closed.
This standard refers to the inspection of steel castings on valves, fittings, flanges, and other piping components. It provides a uniform means of identifying different types of surface irregularities.
Valve Testing Methods
A valve test is often performed with three parties in attendance. The manufacturer, the purchaser, and a third party agent. The inspection should be documented and issued as a report afterwards.
Shell Test
In the shell test, the valve is partially open and subjected to hydrostatic pressure at a 50% higher level than its rated working pressure. The fluid must be within a certain temperature range.
If the valve is made of stainless steel, the chloride ion content cannot be more than 100 ppm.
Seat Leak
The seat leak test involves closing the valve entirely, and subjecting it to hydrostatic pressure while the outlet side is monitored for leaks. The pressure must be at least 110% of its maximum allowable pressure. The fluid must be 100 degrees Fahrenheit. The test lasts for 1 minute. To pass the test, the valve must not leak from the stem or packing, but a small amount of leakage from the disc or seat is acceptable.
Backseat Test
For the backseat test, the valve is fully opened, but the ends are closed. Like with the seat leak test, the pressure must be at least 110% of its maximum allowable pressure, and the fluid must be 100 degrees Fahrenheit.
The duration of the test depends on the size of the valve. For one that is less than 2 inches, the test lasts for 15 seconds. For a valve larger than 2 inches, the test lasts for 60 seconds. There must be no leakage during the test.
Allowable Leakage Rates
The API differentiates check valves from other types of valves because check valves depend on pressure to seal, which makes them more difficult to seal. API 598 states that no visible leakage is allowed through the external surface for shell and backseat tests. The external surface means the body, the body liner, and the joints of valves. For resilient seated valves, standards do not allow leakage at all.
For metal-to-metal check valves, 2 drops of liquid or 3 drops of gas are allowed to leak per minute. This is the case regardless of the size of the valve. For metal-to-metal valves of any other type, the acceptable number of drops varies with the size. The smallest type of valve, less than 2 inches, may have 1 drop of liquid or gas per minute. The largest size, greater than 12 inches, may have 28 drops of liquid per minute, or 56 drops of gas per minute.
The API publishes charts specifying the allowable number of drops for different sizes.
Inspection and Testing
A valve test is an important way of ensuring the efficient and safe operation of industrial processes. These processes depend on valves performing with precision to regulate temperature, pressure, and flow. The standards also promote product quality and safety. As more companies source their products globally now, testing has become paramount to the customer’s ability to feel confident about their purchase.
Different testing methods require different fluids. The high-pressure closure and shell tests involve air, inert gas, kerosene, water, or any other fluid that is of equal or lower viscosity than water. Low-pressure and backseat pressure tests are done with air and inert gas.
Where to Find Reliable Valves
It’s important to look for a manufacturer who uses these valve testing methods to make sure you’re getting a good product.
If you are looking for a valve product that meets these qualifications, contact Everlasting Valves to learn about our service value and innovative designs. Our open body design seals better the longer you use it, so you can be sure it will meet these standards.